I decided to model the broken sunroof drain in Fusion360, and then print it on my Prusa printer. Surely this would be a “quick” and “easy” alternative to spending big bux? It worked out in the end, but the process was really rather frustrating: Fusion is difficult for complex shapes (for amateurs like me), and 3-D printing still seems much more an art than a science.
(If you want to download this part to print for yourself, find it on “thingiverse” at this URL: www.thingiverse.com/thing:3907837 )
I discovered just how hard it is to accurately measure a thing which is all curved edges and random shapes. I understand that pros who reproduce parts invariably use a 3-d scanner to get the initial shape, and while that sounds delightful, I assume that said activity is also as much an art as the rest of this process–plus undoubtedly requires $$$$ more equipment. So, no.
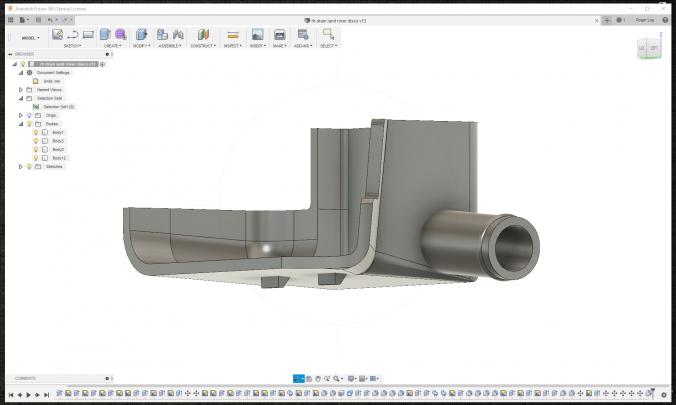
I think modelling the part took about eight hours, all-in, but it may have been more than that. Thankfully this is a hobby, or that would have been a few hundred dollars of my time. (Of course, if anyone was willing to pay for my time at the moment, I might have opted to buy the part, but time is something I have right now…)
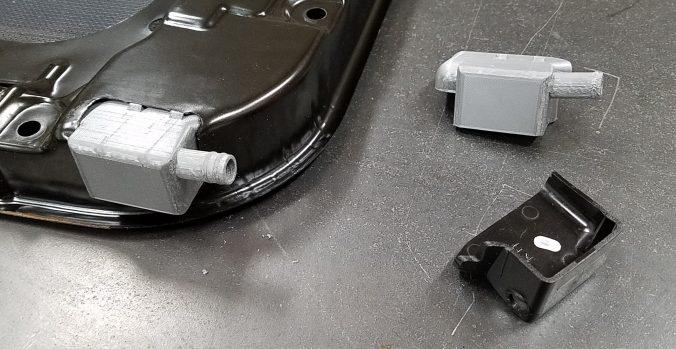
I originally printed the part using PLA filament, which, as it turns out, has a very low plasticity temperature, making it completely unsuitable to life in the roof of a car, where it can get well over 150F. So I ordered a spool of PETG filament…which is probably not as good a choice as ABS, but printing ABS requires a vent hood, which I don’t have. PETG is a decent second choice, I gather. I hope.
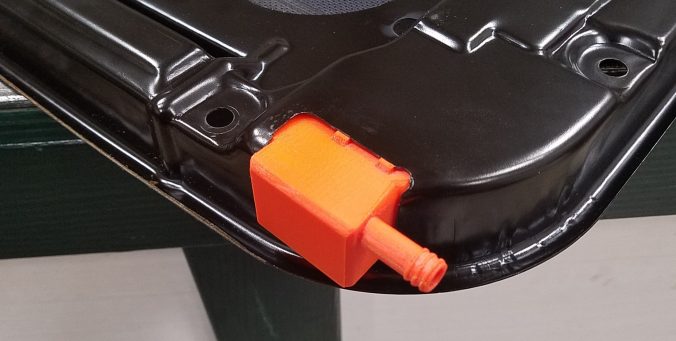
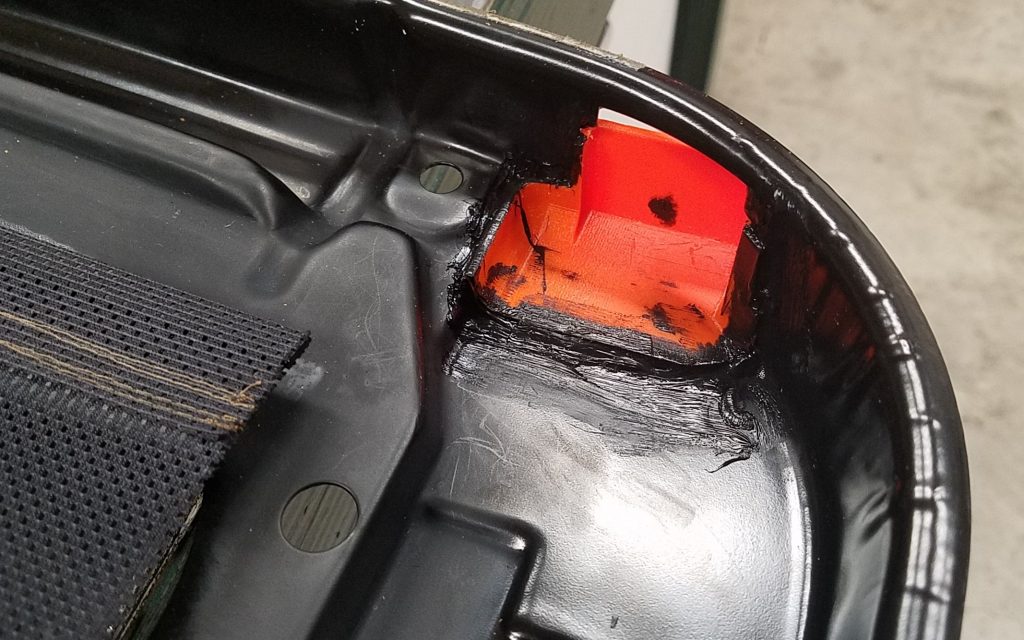
PETG squirts out at a hotter temperature, and my printer was getting thermal runaway errors when trying to print using the Windows 10 default 3-D printing utility. This drove me bonkers, but I finally tried the slicer and printing utility from Prusa, and that solved the problem. As it turns out, the Microsoft utility simply blasts the print-head fan at 100%, all of the time. The printer, by design, cannot overcome that when printing with a high-temp filament. This is hard-won knowledge on my part…if I had hair before I started I wouldn’t have any now.
The actual printing time was roughly two and half hours, once the final part was sent to the Prusa. (I probably started and had to re-start half a dozen prints, as I either messed up, or the printer decided to be a butt.) I feel like 3-D printing is much less advanced and reliable than it is sold as being…
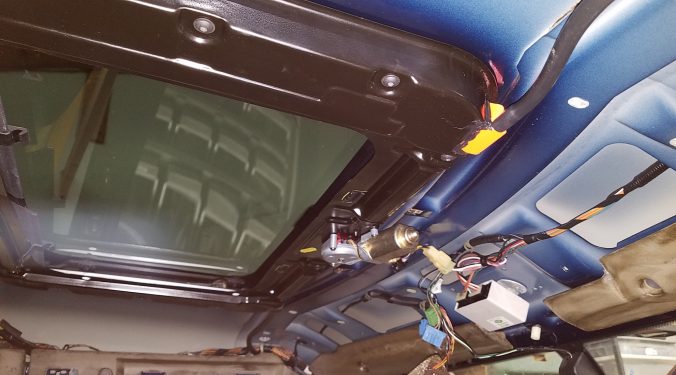
Hopefully this repair will last for a bit. (I would argue that with the sunroof closed, water shouldn’t be entering this pan anyway, but I’m also not really excited to replace the seal, so we’ll find out how effective this all is.)
The headliner cloth should be here mid-week, so hopefully the next post will show that going on the board and the whole thing going back in the car.